Appalachian Organizations Are Working to Make the Region a Hub for Green Manufacturing and Clean Energy
New federal funding will help small and medium-size manufacturers join the emerging circular economy
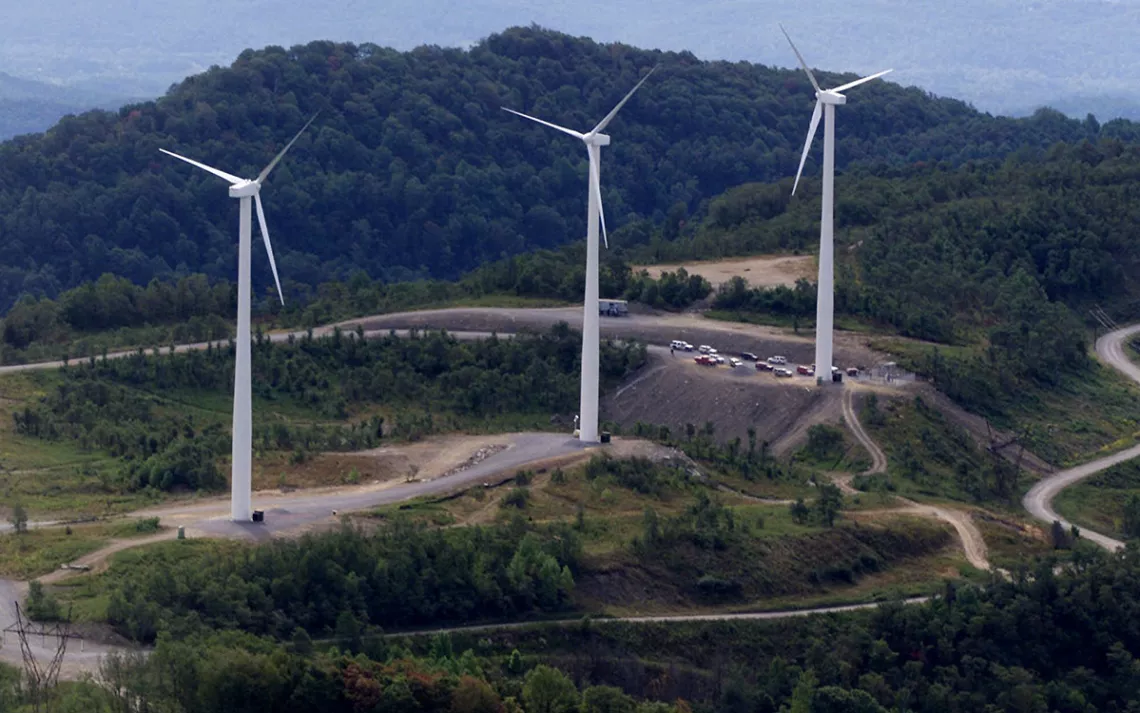
Three windmill turbines sit atop Buffalo Mountain in Oliver Springs, Tennessee. | Photo by Wade Payne, AP file
A Pittsburgh-based coalition is launching a new project to put Appalachia at the front and center of the clean energy transition.
The goal of the $10 million Manufacturing the New Energy Economy in Appalachia project—funded by grant money awarded through the Bipartisan Infrastructure Law—is to remake the region into a national hub for green manufacturing and clean energy. The grant will work to minimize barriers facing small to medium-size traditional manufacturers (defined as those with 500 employees or less) while providing a route for local manufacturers to plug into the burgeoning clean energy supply chain.
Grown from a coalition led by Catalyst Connection, a private consultant and training center for small manufacturers in Pennsylvania, the grant facilitates investments in 14 supply chains: renewables like solar and wind, green building products, circular plastics, and electric vehicle batteries. Over four years, the task force is meant to assist over 1,000 businesses with small grants to help manufacturers become more energy efficient or invest in the training and technical assistance required to manufacture new clean energy products, like a hub for electric vehicle battery technology already expanding across Appalachian states. These businesses can apply for $10,000 mini-grants to cover half the cost of a project associated with improved energy efficiency or for technical assistance to transition into a cleaner supply chain.
The need for such assistance is great, said Tom Reed, director of communications and community outreach for Catalyst Connection, which will work with more than 10,000 manufacturers across the 156 counties under the project’s purview. Reed explained what his organization could achieve when he answered a Zoom call from the inside of an old steel mill that’s been converted into a new office building: “They kept the history [of the mill] while moving forward,” Reed said. “That’s what we try to do too.”
This work is led by the Next Manufacturing Task Force, a manufacturing coalition composed of 10 affiliates across five states, like manufacturing extension partnerships and ReImagine Appalachia, a regional nonprofit founded in 2020 to create in Appalachia an economy that’s good for workers, communities, and the environment.
“The Ohio River Valley, with the right investments, we can be global leaders in the new energy economy,” said Amanda Woodrum, co-director of ReImagine Appalachia. Her organization synthesizes input from diverse stakeholders across the region—including organized labor, racial justice organizations, faith groups, local governments, and federal entities—on how to create a circular economy instead of copying the top-down approach the coal economy brought to the region.
“A big part of our strategy is growing clean and efficient manufacturing in the region, because we think it’s key to creating equivalent jobs to those in the coal industry,” Woodrum said. The organization's circular approach—sustainable manufacturing making sustainable products of the future—looks at existing assets in Appalachia to make one company's waste another company’s raw materials.
Woodrum pointed to a series of examples for how to turn coal liabilities into opportunities, including mining coal ash for rare earth minerals to be used in battery technologies, recycling coal ash into green building materials like cement, and turning acid mine drainage into primer for artisan paints.
Another prime example, according to Reed, is CAB Solar Cable Management, an organization working with blind and disabled employees to produce the ties that hold up the wiring in coal tunnels; the organization has now replaced its supply chain to produce the wiring used beneath the panels at solar farms.
“The coal industry was a good opportunity,” Reed said, “but now [CAB Solar] sees there’s a growing opportunity in renewables.”
Or take New Leaf Justice Enterprises, a housing and technology project in Athens, Ohio, that provides a cutting-edge example of how to use new, green manufacturing technology to solve a social problem in the rural town. The program teaches victims of domestic violence new skills for manufacturing houses, which in turn creates affordable housing.
Jennifer Siefert, director of New Leaf’s Survivor Outreach Advocacy Program for victims of domestic violence, said in domestic violence prevention the best practices for keeping victims from returning to violent relationships was to provide economic security for victims and their families.
“We have to address what happens when people leave our program, so they don’t go into the same community and circumstances that led them here,” said Siefert, who is also the executive director of New Leaf. “When we look in our region, not having access to affordable housing is one of the biggest contributors.”
Siefert teamed up with Chris Sentz, founder of Vitruvian, a company using 3D printing for robotics and advanced manufacturing, to combine their organizations’ skill sets. New Leaf, with the help of Vitruvian and Alquist (a company turning coal waste and fly ash into composite decking and concrete walls) will work to turn the detritus from Appalachia’s past into housing materials.
“The great thing about Appalachia is a lot of materials can be repurposed and taken out of the waste cycle. So we’re not only providing housing and building communities, but we can do it in a sustainable way,” said Sentz, referring to the work of Alquist. “We want to be a beacon of hope to start this kind of reenergizing of rural communities. That’s the overarching vision. We want to educate others to do it as well.”
Together, Siefert and Sentz plan to build 24 advanced housing units on 15 acres slated for housing development by the end of 2026. New Leaf plans to use 3D printing, recycled waste materials, and renewable energy systems to create affordable and sustainable housing. The development will also include a workforce development center to train new workers in a housing and manufacturing hub, including workers leaving Siefert’s Survivor Outreach Advocacy Program.
“There’s not a silver bullet to fix the housing crisis,” said Siefert. “It’s a gnarly problem with lots of dynamics at play. We deploy silver buckshot where we create materials and value engineering and social engineering to try and tackle this problem with different types of robots, materials, and social interventions, and we’re really trying to pull it all together.”
While their program has not applied for funding through the newly awarded grant, Woodrum said Siefert’s project is a prime example of a project that could apply for additional funding.
“Appalachia relied heavily on coal, and all of us living in those regions know the coal industry has been on the decline,” said Petra Mitchell, president and CEO of Catalyst Connection. “Opportunities and programs like this [grant] offer new growth opportunities.”